


As a factory specializing in low-pressure die casting for electric vehicle inverters, we pride ourselves on our precision and efficiency. Our process utilizes low-pressure casting techniques, ensuring that each component meets the highest standards of quality and durability. We specialize in serving the electric vehicle industry, understanding the unique demands of inverter production. By selecting aluminum as our primary material, we achieve a balance of lightweight design and structural strength in our finished products. Our commitment to excellence extends beyond production, as we prioritize customer satisfaction and timely delivery. With a focus on innovation and reliability, we are your trusted partner for all your electric vehicle inverter casting needs. Please feel welcome to contact us.
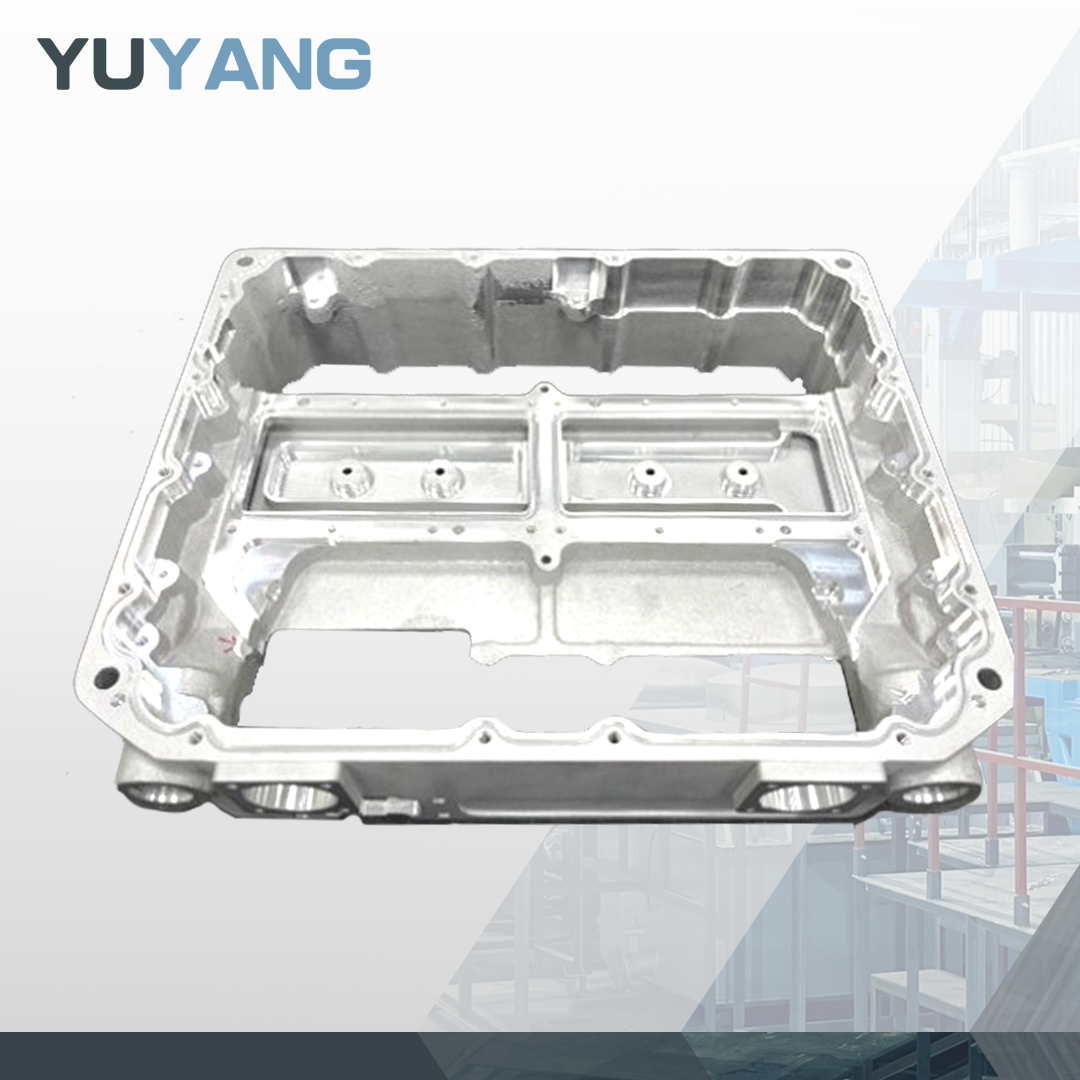
- Low pressure casting
- Electric vehicle industry, inverter
- To achieve lightweight and structural strength in finished products, aluminum is selected for manufacturing.
- The principle of low pressure casting is to introduce dry compressed air with controllable pressure into a preheated furnace containing molten metal. The air is injected onto the surface of the molten metal at a certain temperature, causing the molten metal to rise along the riser tube and enter the mold cavity through a runner. After the mold cavity is filled with molten metal, the air pressure is increased to maintain the gas pressure on the liquid surface until the casting is completely solidified. Then, the pressure is released, allowing the un-solidified molten metal in the riser tube and runner to return to the preheated furnace. This completes a casting process, and the desired casting is obtained after the mold is opened.
- Material: A356.0-T6
- Weight: 6.8 kgs
As a factory specializing in low-pressure die casting for electric vehicle inverters, we take pride in our commitment to quality and innovation. Our process utilizes the latest technology to achieve lightweight and structurally strong finished products, making us a reliable choice for the electric vehicle industry.
Our casting process revolves around the principle of low-pressure casting, where dry compressed air with controllable pressure is introduced into a preheated furnace containing molten metal. The air is then injected onto the surface of the molten metal at a certain temperature, causing it to rise along the riser tube and enter the mold cavity through a runner. Once the mold cavity is filled, the air pressure is increased to maintain the gas pressure on the liquid surface until the casting is completely solidified. Subsequently, the pressure is released, allowing the unsolidified molten metal in the riser tube and runner to return to the furnace. This meticulous process ensures that each casting meets the highest standards of quality and precision.
We specialize in using A356.0-T6 aluminum alloy, which undergoes a heat treatment process to enhance its mechanical properties. This aluminum alloy is known for its excellent castability, machinability, and corrosion resistance, making it ideal for applications in the electric vehicle industry. Each casting weighs approximately 6.8 kilograms, making them lightweight yet durable. A356.0-T6 aluminum is A356.0 aluminum in the T6 temper. To achieve this temper, the metal is solution heat treatment and artificial aging until it meets the standard mechanical property requirements.
In addition to our commitment to quality, we prioritize sustainability in our manufacturing processes. We strive to minimize waste and energy consumption to ensure that our operations are environmentally friendly. With our dedication to excellence and sustainability, we are proud to be a leading provider of low-pressure die casting solutions for electric vehicle inverters.
Our factory is equipped with state-of-the-art machinery and a team of skilled professionals who are dedicated to delivering superior products. We adhere to strict quality control measures at every stage of the manufacturing process, ensuring that each casting meets the highest standards of performance and reliability.
Furthermore, we understand the importance of collaboration and communication with our clients. We work closely with them to understand their specific requirements and provide customized solutions that meet their needs. Our customer-centric approach has helped us build long-lasting relationships with our clients who trust us to consistently deliver high-quality products consistently.
In conclusion, our factory is a trusted partner for companies in the electric vehicle industry seeking high-quality, low-pressure die casting solutions for inverters. With our commitment to quality, innovation, and sustainability, we are confident in our ability to meet the evolving needs of our clients and contribute to the advancement of the electric vehicle industry.
Our products in different indstries | Products and Services | |||||
FC/FCD casting | Alumimum alloy casting | Welding | Precision machining | Surface treatment | Assembling | |
Automobile Industry | ● | ● | ||||
Aeospace Industry | ● | |||||
Energy Equipment Industry | ● | ● | ● | ● | ● | ● |
Power Transmission Industry | ● | ● | ● | ● | ● | |
Machinery Equipment Industry | ● | ● | ● | ● | ● | ● |
Air Conditioning Equipment Industry | ● | ● | ● | ● | ● | |
Medical Equipment Industry | ● | ● | ||||
Electronics Components Industry | ● | ● | ● | ● | ● | |
Automation and Robotics Industry | ● | ● | ● |
Aluminum Casting Facility | ||||||||||
Brand | Type | Aquire Date | SN / Spec. | Process Capability | Appliance | Production Line Configuration | ||||
Toyosaki | Resin Sand Recycling Equipment | 2010/10 | UDC-89PR | 5T/Hr | Furan Resin | Sand Mold Line - Molding | ||||
Toyosaki | Resin Sand Mixing Equipment | 2010/10 | Customized | 10T/Hr | Furan Resin | Sand Mold Line - Molding | ||||
Toyosaki | Resin Sand Mixing Equipment | 2010/10 | Customized | 3T/Hr | Furan Resin | Sand Mold Line - Molding | ||||
Jnhaomai | Low Pressure Casting Equipment | 2011/03 | JZ455-500 | 500Kg | Aluminum | Sand Mold / Metal Mold Hybrid Line - Casting | ||||
Jet-Shine | Low Pressure Casting Equipment | 2015/03 | JZ455-300 | 300Kg | Aluminum | Metal Mold Line - Casting | ||||
Jet-Shine | Low Pressure Casting Equipment | 2017/8 | Customized | 300Kg | Aluminum | Metal Mold Line - Casting | ||||
Jet-Shine | Low Pressure Casting Equipment | 2018/3 | Customized | 300Kg | Aluminum | Metal Mold Line - Casting | ||||
Jet-Shine | Low Pressure Casting Equipment | 2022/12 | Customized | 700Kg | Aluminum | Sand Mold / Metal Mold Hybrid Line - Casting | ||||
Jet-Shine | Low Pressure Casting Equipment | 2022/12 | Customized | 700Kg | Aluminum | Sand Mold / Metal Mold Hybrid Line - Casting | ||||
Jnhaomai | Mobile Degassing Equipment | 2011/03 | Customized | ─ | Aluminum | Sand Mold Line - Smelting | ||||
Kanghao | Hanging Degassing Equipment | 2017/05 | Customized | ─ | Aluminum | Metal Mold Line - Smelting | ||||
HERSCHAL | Vacuum Hydrogen Meter | 2011/03 | GAS-TECHⅡ | ─ | Aluminum | Sand Mold / Metal Mold Line - Smelting |
Inspection Facility | ||||||||||
Brand | Type |
This is a notification message!
|